Many manufacturers face the challenge of selecting a finishing process that meets high standards while also being cost-effective. The answer could be powder coating—a modern solution designed to address these concerns.
Powder coating is a dry finishing process where electrostatically charged powder particles are applied to a surface and then cured under heat. This creates a tough, long-lasting finish that is far superior to conventional liquid paint. It’s widely used across various industries due to its durability, efficiency, and environmental benefits.
Why is powder coating becoming the preferred choice for so many industries? Let’s explore the key benefits and applications.
How Powder Coating Sticks to Surfaces
Powder coating can be applied using several techniques, each with its own advantages and specific use cases. The choice of method depends on factors such as the size and shape of the object, the type of powder used, and the desired finish. Here are some of the primary methods used for applying powder coatings:
1. Electrostatic Spray Deposition (ESD)
This is the most commonly used method for applying powder coatings. In this process, the powder particles are electrostatically charged as they are sprayed onto the grounded surface of the object. The charged particles adhere to the surface, forming an even coating. Once applied, the powder is cured in an oven, where it melts and forms a continuous, durable film.
- Advantages: Suitable for a wide range of shapes and sizes, high efficiency, minimal waste.
- Applications: Commonly used for automotive parts, household appliances, and architectural elements.
2. Fluidized Bed Coating
In this method, the part is preheated and then dipped into a fluidized bed of powder particles. The heat causes the powder to melt and adhere to the surface, forming a thick, uniform coating. This method is particularly useful for achieving very thick coatings in a single application.
- Advantages: Excellent for achieving thick, uniform coatings; ideal for simple shapes.
- Applications: Used for coating metal parts such as tool handles, dishwasher racks, and heavy-duty machinery components.
3. Electrostatic Fluidized Bed
This method combines elements of both fluidized bed and electrostatic spray techniques. The powder is fluidized and simultaneously charged as it is applied to the part. This allows for a more controlled application, making it suitable for coating parts with complex shapes or for achieving a more even thickness.
- Advantages: Better control over coating thickness; effective for complex geometries.
- Applications: Used in applications where precision and uniform coating are essential, such as in certain electronic components and automotive parts.
4. Air Spraying
Although less common, air spraying can be used to apply powder coatings, especially in situations where electrostatic methods are not suitable. The powder is suspended in air and blown onto the surface. This method is often used for specialty applications where a very thin coating is needed.
- Advantages: Capable of applying very thin coatings; useful for specific applications.
- Applications: Often used in coating small, intricate parts or in situations where precise control over coating thickness is required.
5. Flame Spraying
In flame spraying, the powder is melted in a flame and then sprayed onto the surface of the object. This method is typically used for applying coatings to very large surfaces or in outdoor environments where other methods may not be practical.
- Advantages: Can be used in outdoor or large-scale applications; provides a robust coating.
- Applications: Often used for anti-corrosion coatings on large structures, such as bridges, pipelines, and outdoor machinery.
What Is Powder Coating Made Of?
Powder coating is composed of several key components that work together to create a durable and high-performance finish. The primary ingredients include resins, curing agents, pigments, fillers, and various additives. These components are carefully formulated to ensure optimal performance, durability, and aesthetic appeal.
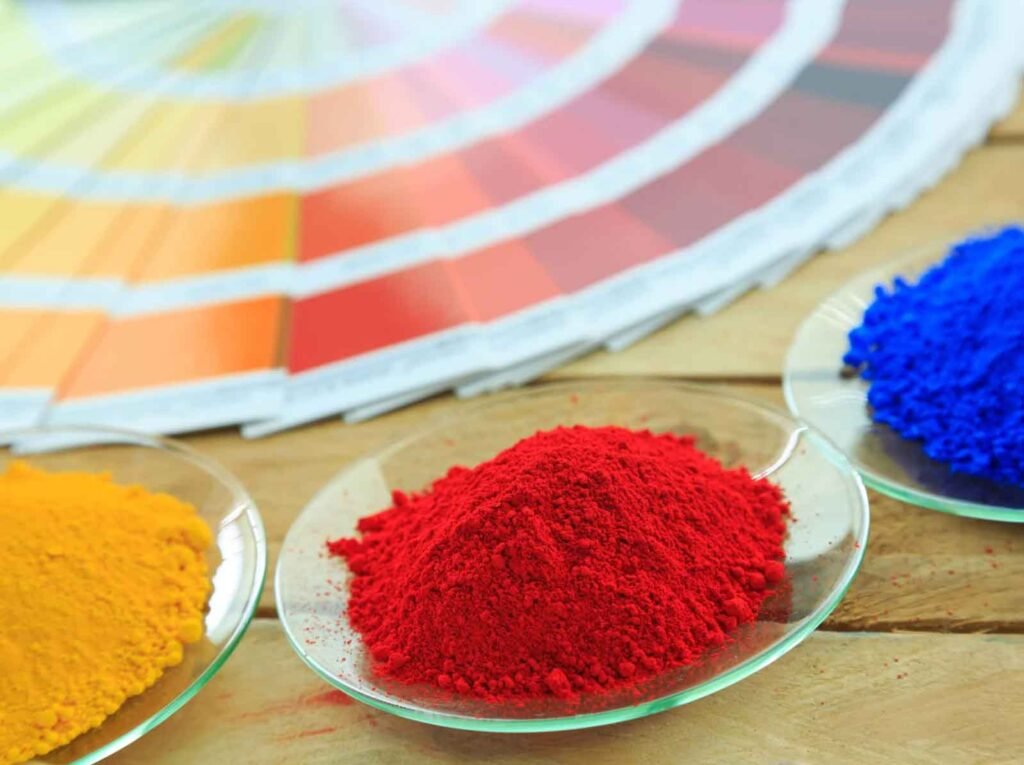
Resins
Resins are the backbone of any powder coating. They can be broadly classified into two types: thermosetting and thermoplastic.
- Thermosetting Resins: These resins undergo a chemical reaction during the curing process, forming a hard, permanent finish. Once cured, they cannot be remelted. Thermosetting resins commonly used in powder coatings include epoxy, polyester, and acrylic resins.
- Thermoplastic Resins: Unlike thermosetting resins, thermoplastic resins do not undergo a chemical change when heated. They melt and flow when exposed to heat and harden upon cooling. This type of resin can be remelted and reshaped multiple times. Common thermoplastic resins include polyvinyl chloride (PVC), polyethylene, and nylon.
Curing Agents
Curing agents, also known as hardeners, are essential in thermosetting powder coatings. They react with the resins during the curing process to form a strong, cross-linked polymer structure. This reaction is what gives thermosetting powder coatings their durability and chemical resistance.
Pigments
Pigments are used to impart color to the powder coating. They also play a role in providing UV protection, corrosion resistance, and overall aesthetic quality. The type and amount of pigment used can affect the final appearance and performance of the coating.
Fillers
Fillers are added to powder coatings to improve their mechanical properties and reduce costs. They can increase the hardness and rigidity of the coating while also providing additional benefits like improved wear resistance and surface smoothness.
Additives
Additives, though used in small amounts, play a crucial role in the overall performance of powder coatings. They can influence the flow, leveling, and curing characteristics of the coating. Common additives include flow agents, degassing agents, dispersing agents, and matting agents. These additives help to achieve a consistent, high-quality finish and can also enhance specific properties such as gloss, texture, and UV stability.
How are Powder Coatings Manufactured?
The manufacturing of powder coatings is a carefully controlled process that involves several stages, each crucial to ensuring the quality and performance of the final product. The process can be broadly divided into the following steps:
1. Pre-mixing
The process begins with the pre-mixing of the raw materials. Resins, curing agents, pigments, fillers, and additives are weighed and mixed together to create a homogenous blend. This step ensures that all components are evenly distributed before further processing.
2. Extrusion
The blended materials are then fed into an extruder, where they are heated and mixed under high pressure. The heat causes the materials to melt and form a uniform, molten mixture. The extrusion process ensures that the raw materials are thoroughly combined and that the chemical reactions between the resin and curing agents are initiated.
3. Cooling and Crushing
After extrusion, the molten mixture is rapidly cooled on a cooling belt or roller, solidifying it into thin sheets. These sheets are then broken into smaller, manageable pieces through a process called crushing. The resulting solid mass is now ready for the next stage of processing.
4. Milling
The crushed material is ground into a fine powder through a process known as milling. The particle size of the powder is a critical factor in determining the finish quality, application efficiency, and overall performance of the coating. Typically, the powder particles range between 10 to 100 microns in size.
5. Sieving
Once milled, the powder undergoes a sieving process to ensure uniform particle size distribution. This step is vital for achieving consistent application and coating performance. Any oversized particles or contaminants are removed, leaving behind a fine, consistent powder ready for application.
6. Packaging
Finally, the finished powder is packaged in airtight containers to prevent contamination and moisture absorption. Proper packaging ensures that the powder remains in optimal condition during storage and transportation until it is ready for use.
How Powder Coating Protects Surfaces
Powder coating is renowned for its ability to provide robust protection to a wide variety of surfaces. Its protective properties come from the way it forms a tough, continuous film that adheres tightly to the substrate. Here’s how powder coating works to protect surfaces:
1. Barrier Protection
Powder coating acts as a physical barrier between the underlying material and environmental factors like moisture, chemicals, and UV radiation. The coating prevents water and oxygen from reaching the substrate, which is crucial in preventing rust and corrosion. This is particularly important for metals that are prone to oxidization.
- Example: Powder-coated steel is widely used in outdoor applications, such as fences and gates, where it resists corrosion much better than uncoated or painted steel.
2. Chemical Resistance
Powder coatings are formulated to withstand exposure to harsh chemicals without degrading. This makes them ideal for industrial applications where surfaces are frequently exposed to solvents, acids, and other corrosive substances.
- Example: Powder-coated machinery parts are often used in chemical plants and manufacturing facilities where they must endure exposure to corrosive agents.
3. Impact and Abrasion Resistance
The curing process of powder coating creates a hard, dense finish that is highly resistant to physical impacts and abrasions. This durability ensures that surfaces maintain their integrity and appearance even in high-traffic or harsh environments.
- Example: Automotive parts, such as wheels and bumpers, are often powder-coated to withstand the rigors of the road, including stone chips, road debris, and frequent use.
4. UV Resistance
Certain types of powder coatings, particularly polyester and polyurethane powders, are designed to resist UV radiation from the sun. This UV resistance prevents the coating from fading, chalking, or deteriorating over time, making it ideal for outdoor applications.
- Example: Outdoor furniture and architectural components like window frames and railings are often powder-coated to ensure long-lasting color and finish even under constant sun exposure.
5. Moisture Protection
By preventing moisture from penetrating the surface, powder coating helps to protect materials from rust and other forms of water damage. The uniform coverage achieved with powder coating ensures that even edges and corners are well-protected.
- Example: Powder-coated piping systems, especially those used in water treatment plants, benefit from this moisture barrier, reducing the risk of rust and extending the service life of the pipes.
6. Resistance to Wear and Tear
Powder coatings provide a durable finish that can withstand everyday wear and tear, including scratches, scuffs, and dents. This makes them an excellent choice for products that see frequent use or exposure to rough conditions.
- Example: Office furniture, like desks and chairs, often features powder-coated surfaces that remain in good condition despite constant use.
Possible Applications for Powder Coatings
Powder coatings are incredibly versatile, finding applications across a wide range of industries due to their durability, aesthetic flexibility, and environmental benefits. Here are some of the key application areas and the types of powder coatings typically used:
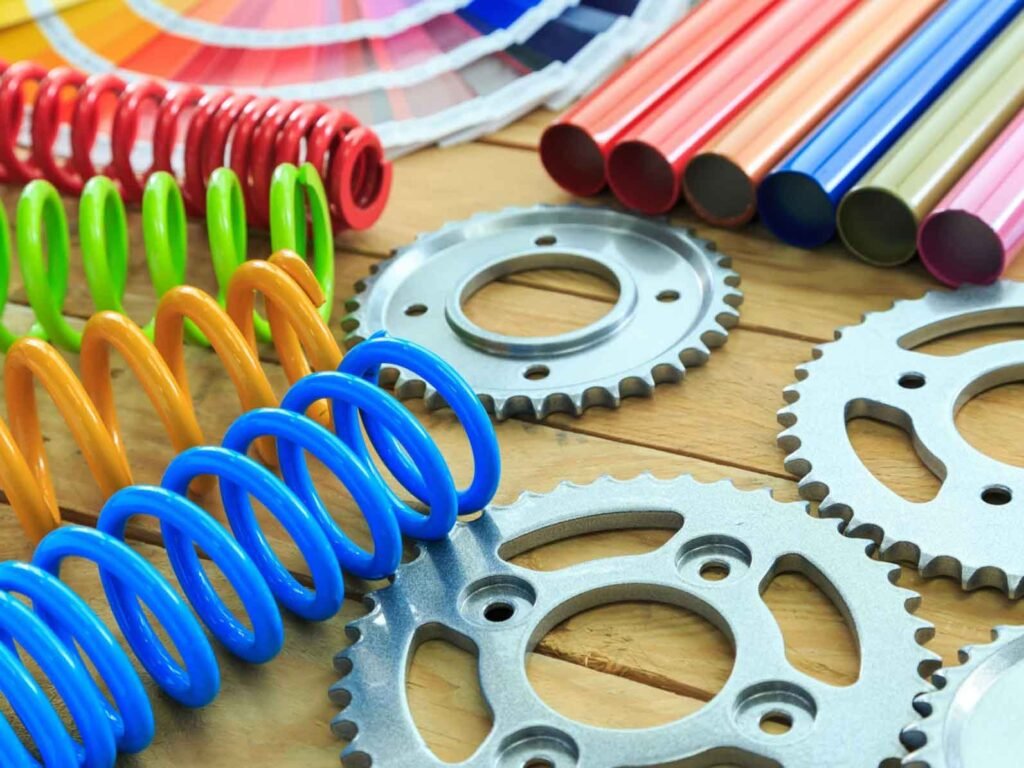
Home Appliances
- Indoor Appliances: Refrigerators, washing machines, fans, rice cookers, and other household items are often coated with polyester and epoxy powder coatings. These coatings provide excellent protection against wear and tear, ensuring the longevity of the appliances.
- Outdoor Appliances: Air conditioner outdoor units and other appliances exposed to the elements use polyester powder coatings for their superior UV and weather resistance.
Automobiles and Transportation Vehicles
- Automotive Coatings: Components such as bumpers, wheels, and body panels are often coated with polyester, polyurethane, and epoxy powder coatings for their durability and resistance to harsh environmental conditions.
- Railway Passenger Cars and Buses: Interior decorations often utilize polyester or epoxy powder coatings for their aesthetic appeal and durability.
- Motorcycles and Bicycles: These vehicles typically use polyester and polyurethane powder coatings for both protection and aesthetic purposes.
- Primers and Outdoor Accessories: Items such as automotive primers and accessories exposed to the outdoors often use epoxy and epoxy-polyester powder coatings for enhanced corrosion resistance.
Building Materials
- Aluminum Profiles, Steel Doors, and Windows: These structural components, especially those used outdoors, benefit from polyester and polyurethane powder coatings for their weather resistance and durability.
- Steel Bars: These are commonly coated with epoxy powder coatings to protect against corrosion and increase structural integrity.
Pipes and Anti-Corrosion Applications
- Oil and Natural Gas Pipelines: These critical infrastructure elements use epoxy and polyethylene powder coatings for their outstanding corrosion resistance and durability.
- Cross-Sea Bridge Cable Pipelines: Epoxy powder coatings are used for their excellent protective qualities in harsh marine environments.
- Chemical Industry Pipelines: Large ship oil pipelines and chemical transport pipelines utilize epoxy and polyethylene powder coatings for their chemical resistance.
- Drinking Water Pipelines: Polyurethane and polyethylene powder coatings are chosen for their safety and durability in potable water applications.
Instruments and Telecommunication Equipment
- Outdoor Telecommunication Boxes: Polyester and polyurethane powder coatings provide the necessary protection against weather and environmental factors.
- Indoor Instruments: Meters, switch cabinets, and other indoor telecommunication equipment often use epoxy and polyester powder coatings for their reliability and aesthetic finish.
Metal Components and Metal Products
- Outdoor Products: These are frequently coated with polyester and polyurethane powder coatings for enhanced durability against weather and environmental factors.
- Indoor Products: Items such as furniture, shelving, and various indoor metal components are often finished with epoxy and epoxy-polyester powder coatings for their robust and long-lasting finish.
Furniture and Garden Furniture
- Office Furniture: Office desks, chairs, and other metal furniture use polyester and epoxy-polyester powder coatings for a sleek, professional finish that also provides protection.
- Garden Furniture: Outdoor tables, chairs, and benches are typically coated with polyurethane and epoxy-polyester powder coatings for their ability to withstand the elements.
Transportation Supporting Facilities
- Highway Guardrails and Guardrail Nets: These are coated with polyester, polyurethane, and polyethylene powder coatings for their durability and resistance to environmental damage.
- Traffic Signs with Lights: Polyester and polyurethane powder coatings ensure these signs remain vibrant and corrosion-free in various weather conditions.
Equipment and Tools
- Outdoor Equipment: Heavy machinery and tools used outdoors are coated with polyester and polyurethane powder coatings to provide long-lasting protection.
- Indoor Equipment: Tools and machinery used indoors often feature epoxy and epoxy-polyester powder coatings for a durable, resilient finish.
Non-metallic Material Coatings
- Medium Density Fiberboard (MDF) Panels: These are coated with various thermosetting powder coatings for enhanced durability and aesthetic appeal.
- Glass Bottles: Specialty powder coatings are applied to glass bottles to improve their resistance to impacts and environmental factors.
Advantages and Disadvantages of Powder Coating
When choosing a coating method, understanding both the advantages and disadvantages is crucial. Powder coating offers numerous benefits, but it also has some limitations that must be considered.
Advantages of Powder Coating
Environmentally Friendly
Powder coatings are free from volatile organic compounds (VOCs) and water. This means no harmful chemicals are released during the baking and curing process, helping to keep the air clean. Additionally, it eliminates the need for wastewater treatment, making it a great choice for environmentally-conscious operations.
Safe for Workers
Unlike traditional solvent-based coatings, powder coatings don’t pose health risks to workers. This makes the production and application processes safer and reduces the risk of fires during production, storage, and transport.
Highly Efficient
Powder coatings can be applied in a closed system where any overspray can be collected and reused. This makes the process highly efficient, with some systems achieving up to 99% utilization of the coating material, saving both resources and money.
Effective Application
With powder coating, you can achieve a thick (50-500μm) durable layer in just one application. This reduces the number of coats needed, saving time and space for drying between applications.
Consistent Quality
Powder coating is not affected by weather or seasonal changes, making it reliable year-round. It’s also easy to learn and doesn’t require highly skilled operators. The process avoids common issues like sagging or bubbling, making it ideal for automated production lines.
Superior Durability
Powder coatings use resins with higher molecular weights than those in traditional paints. This results in a tougher, more durable finish that is resistant to chemicals and wear.
Versatile Application Methods
While electrostatic application is the most common method, powder coatings can also be applied using fluidized bed, electrostatic fluidized bed, air spraying, and flame spraying techniques. This versatility makes it suitable for a wide range of applications.
Variety and Flexibility
Powder coatings come in a wide range of colors, textures, and finishes. They can be used for decorative purposes indoors and outdoors, as well as for heavy-duty anti-corrosion applications.
Disadvantages of Powder Coating
Initial Costs
Setting up a powder coating line requires significant initial investment in equipment like spray booths, curing ovens, and recovery systems. This can be costly, especially for smaller operations.
Space Requirements
The equipment and processes take up a lot of space, which might not be feasible for all businesses.
Application Challenges
While powder coating is great for thick layers, applying very thin coatings can be tricky. Coating items with intricate shapes and deep recesses can also be difficult, as the powder might not reach all areas evenly.
Curing Process
The high temperatures required for curing can be unsuitable for heat-sensitive materials. Additionally, curing ovens consume a lot of energy, which can increase operational costs.
Color Consistency
One of the biggest challenges in powder coating is color matching. Unlike solvent-based and water-based paints, you can’t simply mix pigments to achieve the desired color. Switching colors during production can also be time-consuming and cumbersome.
What Is the Powder Coating Process?
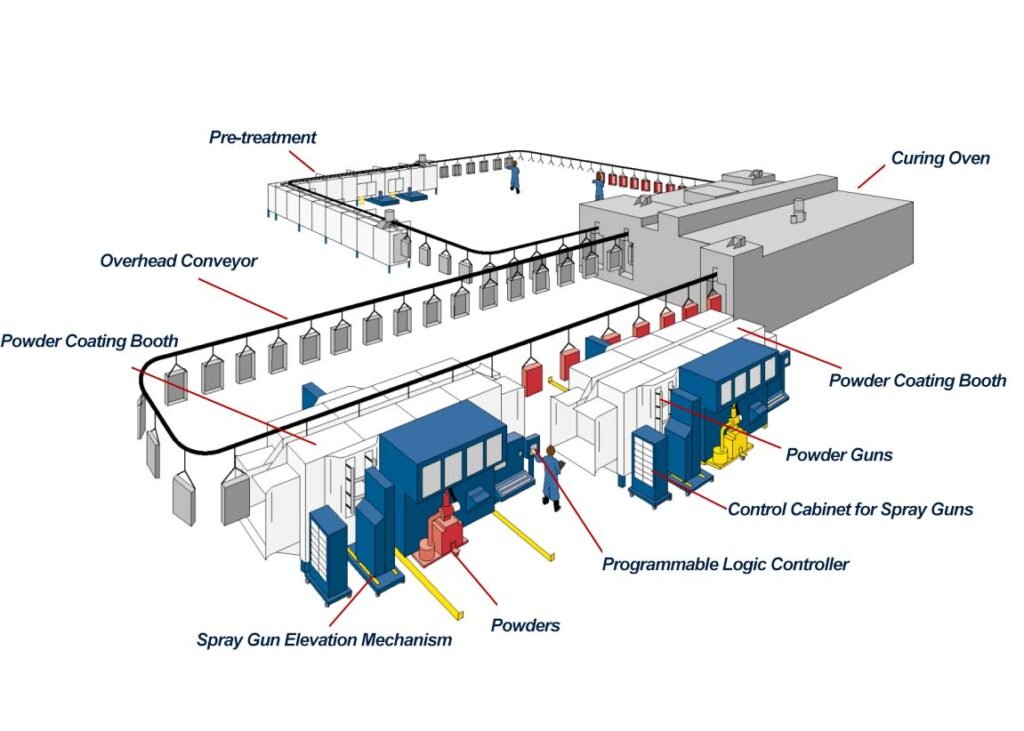
The powder coating process is a multi-step procedure designed to ensure a high-quality, durable finish. Each step is crucial for achieving the desired performance and appearance of the coating. Here’s a detailed look at the powder coating process:
1. Surface Preparation (Pre-treatment)
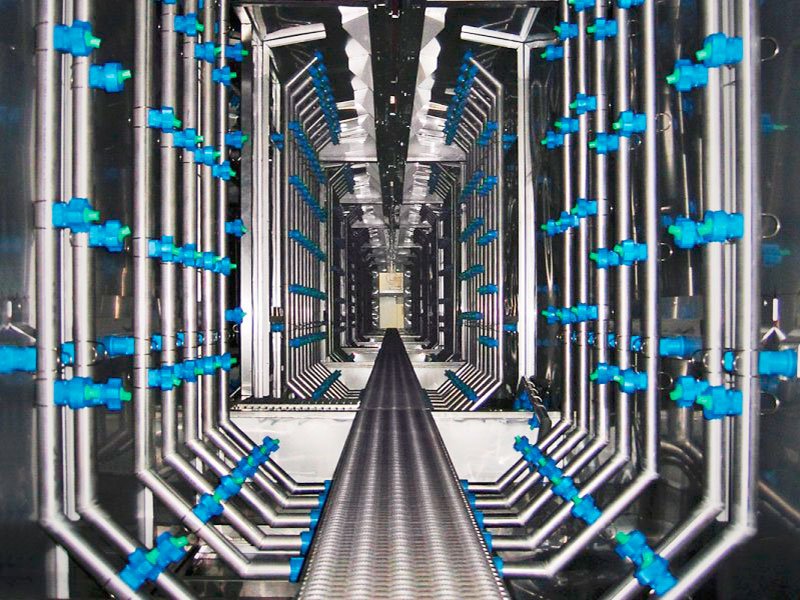
The first and most critical step in the powder coating process is surface preparation. Proper cleaning and treatment of the surface ensure that the powder adheres correctly and the coating performs as expected. This step typically involves the following procedures:
- Cleaning: The surface is cleaned to remove any dirt, oil, grease, or other contaminants. Methods include chemical cleaning, sandblasting, or ultrasonic cleaning, depending on the material and the type of contamination.
- Phosphating or Chromating: These chemical treatments are applied to create a conversion coating that improves the adhesion of the powder and provides additional corrosion resistance.
- Rinsing and Drying: After cleaning and treatment, the surface is thoroughly rinsed and dried to remove any residual chemicals and moisture.
2. Application of the Powder Coating
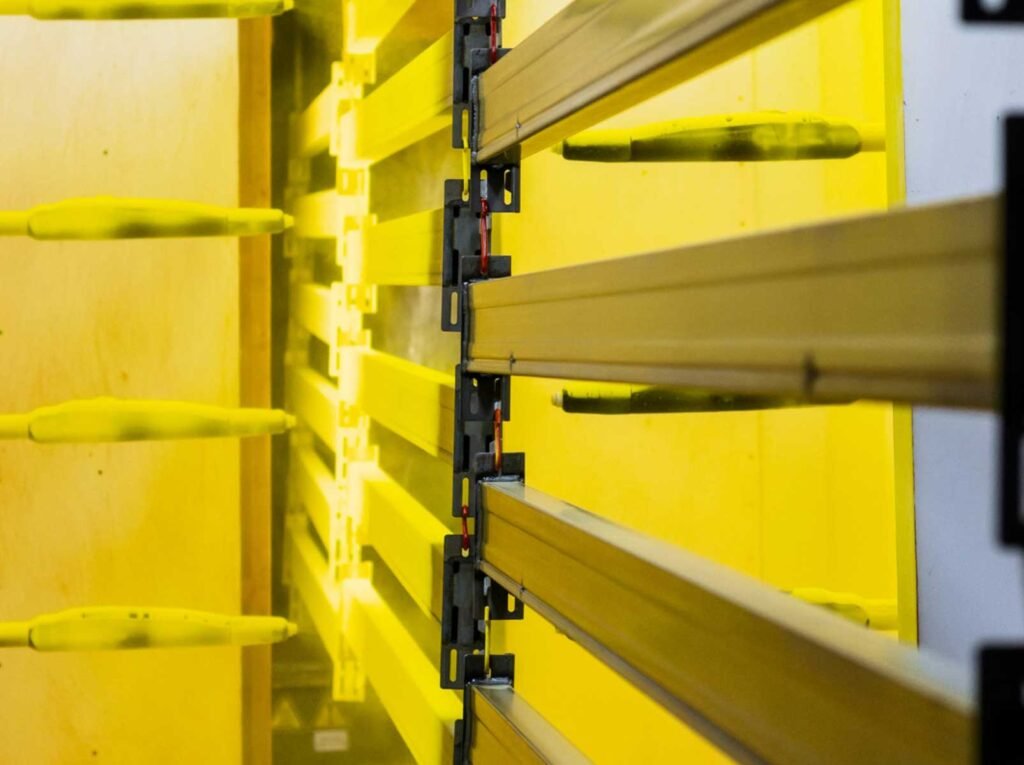
Once the surface is prepared, the powder coating is applied using one of the methods discussed earlier (e.g., Electrostatic Spray Deposition, Fluidized Bed Coating). During this stage, the powder particles adhere to the surface of the part, forming a uniform coating. Key aspects include:
- Powder Selection: The type of powder (thermosetting or thermoplastic) is chosen based on the desired properties of the final coating.
- Application Technique: The chosen method (such as electrostatic spray) is used to apply the powder evenly across the surface. The part is typically grounded to attract the charged powder particles, ensuring a consistent application.
3. Curing
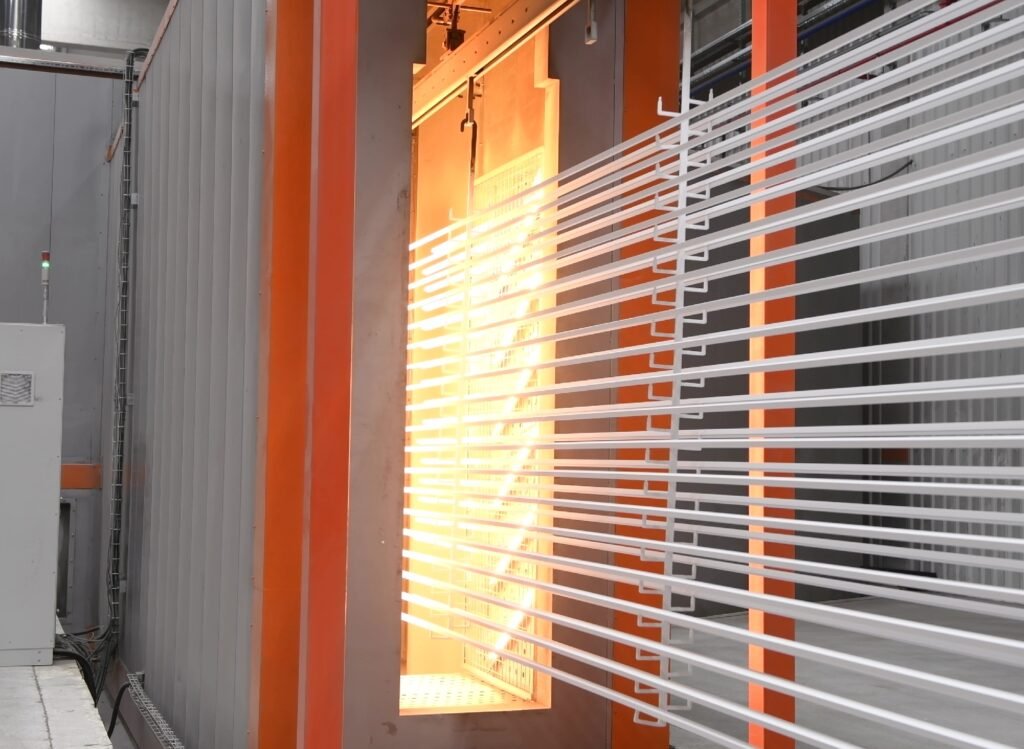
After the powder has been applied, the coated part is moved to a curing oven. In the oven, the powder is heated to a specific temperature, which causes the particles to melt and flow together, forming a smooth, continuous film. The curing temperature and time depend on the powder type and the thickness of the coating.
- Thermosetting Powders: Undergo a chemical reaction during curing that creates a cross-linked polymer structure, resulting in a hard, durable finish.
- Thermoplastic Powders: Melt and flow during heating, then harden upon cooling without undergoing any chemical change.
4. Cooling
Once curing is complete, the part is allowed to cool. This can be done naturally or with the aid of cooling fans to speed up the process. Cooling solidifies the coating, giving it the desired mechanical properties, such as hardness and impact resistance.
- Controlled Cooling: In some cases, controlled cooling is necessary to prevent the coating from cracking or warping, particularly with thicker coatings or specific materials.
5. Inspection
The final step in the powder coating process is inspection. This involves checking the coated part for any defects, such as bubbles, thin spots, or uneven coverage. Several testing methods may be used:
- Visual Inspection: To ensure there are no visible defects or inconsistencies in the coating.
- Thickness Testing: Using tools like micrometers or ultrasonic gauges to measure the thickness of the coating, ensuring it meets specifications.
- Adhesion Testing: To confirm that the coating is securely bonded to the substrate and will not peel or flake under stress.
Once the inspection is complete and the part meets all quality standards, it is ready for packaging or further assembly.
Conclusion
If you’re in the market for high-quality powder coating equipment, we’re here to help. At Tifuls, we specialize in providing state-of-the-art powder coating lines, spray guns, booths, and curing ovens that meet the highest standards of quality and efficiency. Whether you need a fully automated system or a more manual setup, our team can customize a solution to fit your specific needs.
Ready to enhance your production with the best powder coating technology? Contact us today to discuss your requirements and find the perfect equipment for your business.